Artificial intelligence applications are widely used for fault diagnosis by monitoring vibration data. In order for artificial intelligence applications to provide the most efficient results, they need to be trained using data obtained by regular monitoring of machines for long periods and evaluated by experts. As a result of this training, the operating characteristics of the machinery will be recognized and the diagnosis of the potential faults will be possible. However, even during the training process, machine failures must be detected successfully. In such cases, where there is not enough data readily available yet or if it is difficult to obtain working characteristics from experts, a diagnostic technique based on machine mode similarity analysis can be used.
Raw vibration data from the sensors can be converted into meaningful features and using these features, “machine modes” that summarize the operating cycle of a machine can be found. Machine modes indicate important changes that a machine may encounter during its lifetime, such as machine downtime, minor changes in operating conditions, and malfunctions. The extracted modes indicate similar trends for similar machine types used in industry. Therefore, the operating characteristic of a machine for which there is insufficient information or measurements, can be determined using the modes of another machine whose operating characteristics are well known. A process, which could take a lot of time and effort under normal conditions, becomes easy, fast and understandable with mode similarity analysis.
Mode Similarity Analysis
For the mode similarity application, determination of a “donor” machine is the first step. A donor machine is a machine which is well recognized by our artificial intelligence algorithm and it provides the machine mode information to the system. The raw vibration data coming from the donor machine are analyzed with various techniques in time and frequency domains and decomposed into their features. These features are evaluated by the machine learning algorithm and their respective signals are separated into machine modes. The resulting modes are examined by reliability engineers who are experts in the field, in order to determine which operating conditions or fault types they belong to. Simultaneously, the data of the “acceptor” machine, are processed and its features are extracted. Acceptor machine is the machine whose status is desired to be known and to which the machine modes will be transferred. An acceptor machine should have a similar drivetrain to the donor machine. Finally, the failure modes of the acceptor machine can be determined by analyzing the similarity between the defective modes of the donor and available measurements of the acceptor machine. In this application, a real machine can be used as a donor as well as a readily available, comprehensive mode library.
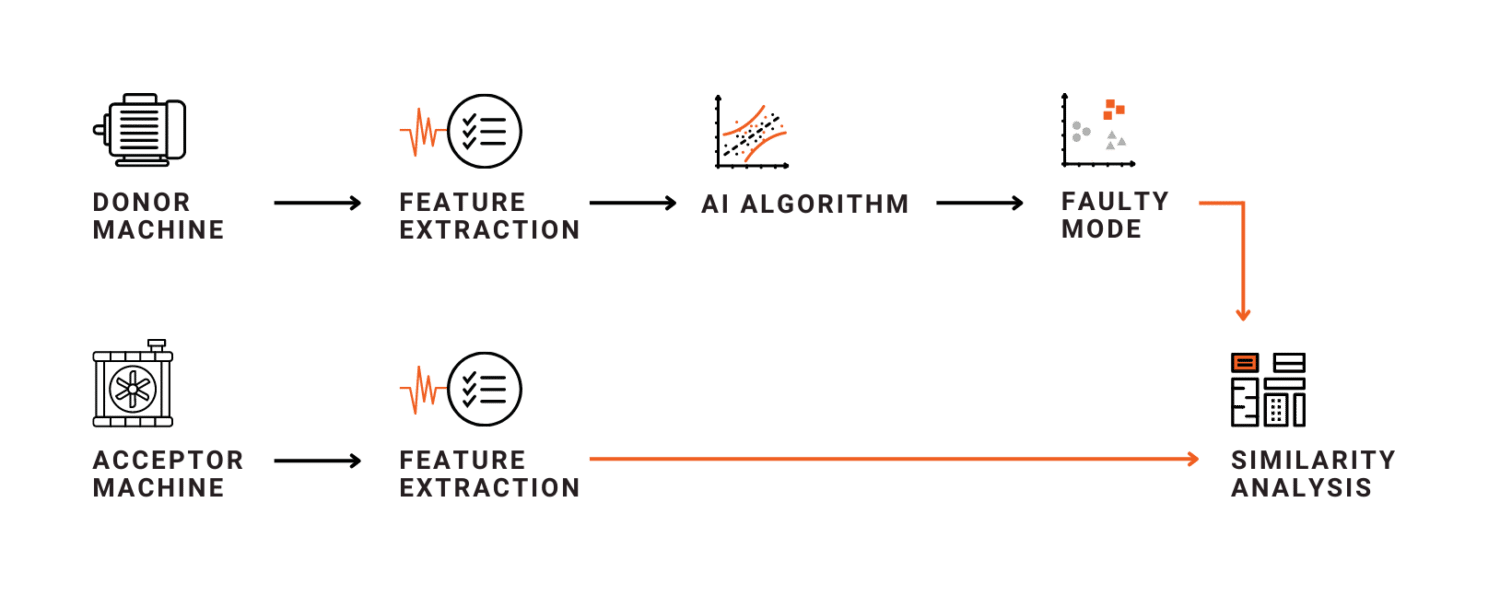
Fig. 1 Mode Similarity Analysis Flow
Example Application
We can demonstrate this technique more clearly with an application. First of all, let’s consider a centrifugal pump driven by a 250 kW electric motor as the donor machine, whose operating characteristics are fully defined in our mode pool. As the acceptor machine, a fan driven by an electric motor with a capacity of 200 kW will be considered. Although the basic features of these two machines are very different, if the raw vibration data is analyzed correctly, it will be possible to transfer the machine modes by establishing a correlation between them. Both of the selected machines have variable rotational speeds. Therefore, the resonance situation, which has a critical importance in machine health, has been chosen as the type of failure to be determined in the scope of the example. However, a similar application can be applied for many other failure root causes.
The 3-axis vibration data as well as the measurement specific RPM (revolutions per minute) values were collected from the donor machine. Meaningful features were extracted from the raw data and were fed into the machine learning algorithm. The algorithm outputs the measurements divided into machine modes. The mode that shows the resonance characteristic and the measurements included in this mode were marked for comparison with the acceptor machine.
Fig. 2 3 Axis VRMS Data with Respect to Measurement Index for the Donor Machine, Separated Into Machine Modes Including the Resonance Mode
For the acceptor machine, the measurements were collected in the same way and their features were extracted. Then, as a final operation, the measurements of the mode marked as resonance failure in the donor machine and all the measurements of the acceptor machine were fed into the similarity algorithm. The resulting similarity score for each measurement indicates how close the measurement is to the resonance mode. The measurements with the highest score should then be re-examined by the reliability engineer team to fully confirm the failure mode.
In this application, the measurement number 341 has the highest similarity score and is confirmed to show the resonance characteristic for the acceptor machine.
Conclusion
Within the scope of predictive maintenance, even if a machine is still in the recognition process, its operating and failure modes can be determined by making mode similarity comparisons. In this way, it is possible to have an idea on the instant status of many machines without waiting for the initial training and estimation phases, and thus quicker reactions can be given in case of emergencies.
References:
- Şerifoğlu, M. O., Gencer, F. B., Aktaş & A. Ö., Ulusoy, A. E. (2022). Makine Modu Benzerliğini Kullanarak Titreşim Tabanlı Rezonans Teşhisi. Uluslararası Katılımlı Bakım Teknolojileri Kongresi ve Sergisi 20-22 Ekim 2022 Denizli. ISBN: 978-605-01-1546-8
Recommended Blog Posts
September 4, 2023
Powerful Signal Analysis Tools for Vibration Analysis
Predictive maintenance, crucial for machinery reliability, heavily relies on vibration analysis. Techniques like FFT…
September 4, 2023
Rotating Machinery Vibration Analysis
Vibration analysis is a critical tool in various industries like manufacturing, power generation, and transportation.…
September 15, 2022
Understanding Rotating Machinery Data
Machine data is generated by physical attributes and actions of machines, collected by sensors and analyzed for…
August 6, 2021
Envelope Analysis
Bearings are critical elements in rotating machines, they support radial and axial loads, and reduce friction. Real…
May 6, 2021
What is Cepstral Analysis?
Cepstral Analysis, a tool used to detect periodicity in frequency spectrum, can be useful in gearbox fault detection in…
October 9, 2020
How is Fault Detection Performed?
Vibration measurements and analysis, using multiple parameters, can identify developing problems in machinery before…
September 21, 2020
Parameter Selections in Vibration Measurement
Vibration measurements are used to determine the response of machines to forces and identify potential issues. It is…
September 4, 2020
What is Vibration Analysis?
Vibration analysis can be used to discover problems in machines and predict when they might fail. It can significantly…