Motor Current Signature Analysis (MCSA) technique serves as a sophisticated diagnostic tool, allowing engineers to delve deep into the heart of electrical machines and decode their operational health. MCSA operates as a methodical process for scrutinizing and comprehensively tracking the condition of electrical machines. It goes beyond mere monitoring; it serves as a sentinel, poised to detect potential malfunctions before they escalate into critical issues. At its core, MCSA harnesses the power of asynchronous motors as transducers, extracting invaluable insights from the currents coursing through these mechanical powerhouses.
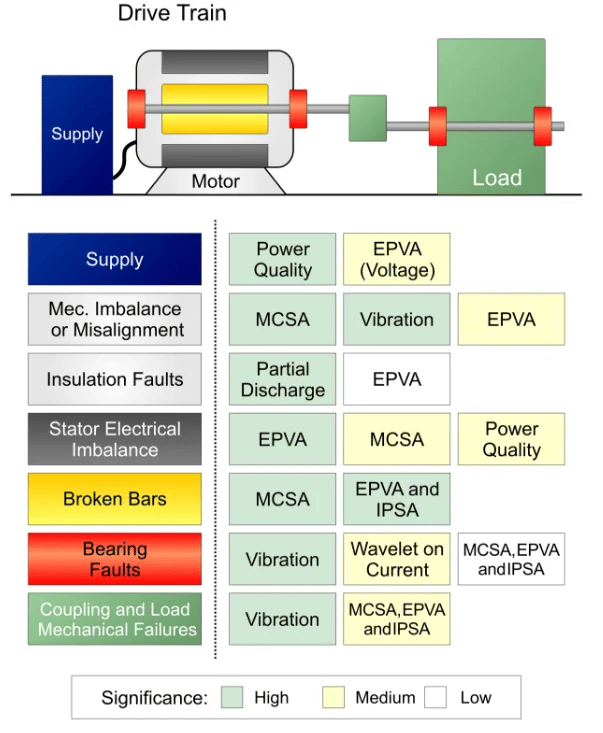
Fig. 1 Faults Detected by Different Methods
Monitoring Electrical Machine Health
In the ever-evolving landscape of industrial engineering, the health of electrical machines is a cornerstone. These machines, vital to the functioning of various industries, demand vigilant oversight to ensure seamless operations. Monitoring their health becomes paramount, akin to a medical check-up for the vital organs of an industrial ecosystem.
The intricate dance of currents within electrical machines provides a wealth of information about their well-being. MCSA continuously observes and analyzes the nuances of motor currents. The importance of this meticulous monitoring extends beyond the immediate; it is a proactive approach that safeguards against potential downtimes and disruptions in industrial processes.
Early Fault Detection with Motor Current Signature Analysis
The significance of early fault detection cannot be overstated. MCSA empowers engineers to identify, with precision, issues ranging from stator winding irregularities to rotor imbalances and beyond. By intervening at the nascent stage of a problem, industries can avoid costly breakdowns, extend the lifespan of machinery, and enhance overall operational efficiency.
Fundamentals of Motor Current Signature Analysis (MCSA)
MCSA: Definition and Purpose
Motor Current Signature Analysis (MCSA) is not just a diagnostic tool. At its core, MCSA involves the extraction and analysis of current signals from asynchronous motors, transforming them into actionable insights. The purpose? To unravel the intricacies of machinery health, foresee potential issues, and pave the way for preemptive corrective measures.
MCSA's Malfunction Detection Capabilities
Motor current signature analysis dissects the current signals from motors with surgical precision, unveiling a comprehensive view of the machinery’s well-being. MCSA can detect malfunctions at their embryonic stage, long before they cast a shadow on operational efficiency.
The methodical approach of MCSA involves collecting current signals, employing a data acquisition device, and subjecting the signals to spectral analysis. This analysis, often facilitated by the Fast Fourier Transform (FFT), unveils the frequency components of the current signal—essentially translating the language of currents into a diagnostic spectrum.
Precision Matters: Identifying Various Types of Issues
MCSA is adept at identifying a spectrum of issues that could compromise performance. From the intricacies of stator winding irregularities to the subtleties of rotor imbalances, MCSA leaves no stone unturned. Its diagnostic gaze extends to coupling issues, load irregularities, efficiency nuances, and even the potential hiccups in bearing functionality.
Imagine foreseeing a bearing issue that might have otherwise resulted in catastrophic failure. MCSA, with its finely tuned capabilities, not only identifies these issues but also distinguishes one from another, providing engineers with a roadmap for targeted interventions.
MCSA Methodology
Asynchronous Motor
At the heart of Motor Current Signature Analysis (MCSA) lies the asynchronous motor, operating not just as a power generator but as a transducer of invaluable data. Asynchronous motors are strategically employed to capture the nuances of current signals coursing through the machinery. They act as interpreters, translating the intricate language of electrical currents into a tangible source of diagnostic information.
The Process of Collecting Current Signals
The journey of MCSA begins with the meticulous collection of current signals from the asynchronous motor. This process involves tapping into the very lifeblood of the machine—its electrical currents. Engineers strategically place sensors or probes at key points in the motor circuitry to capture these signals. The collected data becomes the canvas upon which the health of the machine is painted.
Precision in Data Collection
Data acquisition device serves as the custodian of the gathered current signals, ensuring their accurate capture and transmission for subsequent analysis. The marriage of technology and engineering unfolds as these devices play a pivotal role in preserving the fidelity of the data, enabling engineers to unlock the secrets embedded in the currents.
Signal Conditioning and Spectrum Extraction
Raw current signals hold immense potential but require refinement. Signal conditioning is the process where these raw signals undergo meticulous preparation—adjustments, filtering, and calibration.
The culmination of this journey is the extraction of the spectrum of the signal, an intricate dance performed through tools like the Fast Fourier Transform (FFT). This spectrum, a visual representation of frequency components, is the gateway to diagnosing potential issues. It is in this realm of spectral analysis that patterns emerge, allowing engineers to discern anomalies and predict potential faults.
Analysis of Spectrum in MCSA
Interpretation of the Spectrum of Motor Current
The spectrum of motor current serves as an intricate diagnostic canvas, offering engineers a glimpse into the dynamic orchestra of machinery health. The essence lies in the meticulous interpretation, where engineers meticulously analyze the spectrum to unveil patterns that might serve as harbingers of impending issues or illuminate the symphony of a well-functioning machine. Each peak, trough, and contour within the spectrum becomes a data point, contributing to the holistic understanding of the motor’s operational state.
Explanation of Frequency Components
Within the spectrum, frequency components emerge as fundamental elements. Their magnitudes, representing the amplitude or volume of each frequency, harbor crucial information about the motor’s health and operation. Peaks and valleys within the spectrum delineate the distinctive frequencies present in the motor current. Understanding the significance of these magnitudes is not dissimilar to deciphering a complex score—each frequency contributing to the overall harmony or discord within the machinery.
Significance of Time Waveform Signals in the Frequency Domain
The journey from time waveform signals to the frequency domain marks a transformative juncture in the analysis. This shift is analogous to transitioning from the narrative of a story to the dissection of its structural intricacies. Expressing time waveform signals in the frequency domain unravels latent patterns, laying bare hidden irregularities that may escape notice in the time domain.
Role of Fast Fourier Transform (FFT) in Spectrum Analysis
At the core of spectrum analysis in MCSA resides the Fast Fourier Transform (FFT), a mathematical maestro orchestrating the intricate conversion of time domain signals into their frequency domain counterparts. FFT transforms raw current signals into a comprehensible spectrum. The precision and efficiency of FFT contribute significantly to the diagnostic acumen of MCSA, allowing engineers to navigate the spectrum with mathematical precision and extract actionable insights.
Fig. 2 Monitoring System for Motor Current Signature Analysis
Applications of MCSA
Precision Diagnostics: Discerning Fault Patterns in the Motor
Motor Current Signature Analysis (MCSA) emerges as an astute diagnostician, showcasing unparalleled capabilities in discerning fault patterns intricately woven within the fabric of motor operations. The spectrum, a graphical representation of current signals, transforms into a diagnostic canvas where anomalies and irregularities vividly paint a picture of potential issues. Engineers, armed with the insights derived from spectrum analysis, gain the precision to pinpoint fault patterns that may serve as early indicators of impending problems in the motor. The meticulous analysis of the spectrum enables proactive measures to address potential challenges before they escalate.
Identifying Between Healthy and Unhealthy Motors
Through the analysis of the spectrum, engineers can identify the harmonious currents of a well-functioning motor and contrast them indicative of a motor under duress. This ability to distinguish between the symphony of a healthy motor and the dissonance of an unhealthy one becomes the essence of MCSA’s proactive guardianship over machinery health. The spectrum analysis becomes a diagnostic tool that transcends mere identification, providing a comprehensive understanding of the motor’s operational dynamics.
Anticipating Potential Failure in Specific Components
Beyond the broad strokes of general motor health, MCSA delves into the nuanced intricacies of specific components. It transcends the mere signaling of irregularities and narrows down possibilities, guiding engineers toward specific components that might be teetering on the brink of failure. Whether the challenge lies in stator winding irregularities, rotor imbalances, coupling irregularities, load fluctuations, efficiency nuances, or potential hiccups in bearing functionality—MCSA meticulously lays out a roadmap for targeted interventions. The spectrum analysis becomes a compass, guiding engineers to the precise areas requiring attention and preemptive measures. It transforms MCSA from a diagnostic tool to a strategic partner in ensuring the reliability and longevity of industrial machinery.
Advantages of MCSA
Early Fault Detection Leading to Preventive Maintenance
At the forefront of Motor Current Signature Analysis (MCSA) lies its unparalleled capability for early fault detection. This isn’t just about identifying issues—it’s a proactive stance that allows for preventive maintenance strategies. By unveiling fault patterns in their infancy, MCSA empowers maintenance teams to intervene before issues escalate, mitigating the risk of catastrophic failures. This early detection serves as a cornerstone for a robust preventive maintenance framework, ensuring the continuous health of electrical machines.
Cost Savings Through Timely Repairs and Reduced Downtime
In the dynamic landscape of industrial operations, time is money. MCSA proves to be a financial ally by facilitating timely repairs and minimizing downtime. The ability to predict potential failures enables organizations to plan and execute repairs during scheduled maintenance windows, avoiding unplanned shutdowns that can incur substantial financial losses. This strategic approach to maintenance translates into tangible cost savings, making MCSA not just a diagnostic tool but a financial guardian for industrial enterprises.
Enhanced Reliability and Longevity of Electrical Machines
Reliability is the heartbeat of industrial machinery, and MCSA acts as a vigilant guardian, ensuring a prolonged operational lifespan. By addressing issues in their early stages, this methodology contributes to the overall reliability of electrical machines. The preventive measures initiated through MCSA not only avert breakdowns but also protect the intricate components of the machinery, promoting longevity and sustaining the operational integrity of electrical systems.
Contribution to Overall System Efficiency
By detecting inefficiencies, load fluctuations, and irregularities in components, MCSA allows for targeted interventions that optimize overall system efficiency. This isn’t just about maintaining machinery; it’s about elevating the entire operational ecosystem to peak performance, ensuring that each component operates harmoniously within the system.
Challenges and Limitations
Potential Challenges in Implementing MCSA
While Motor Current Signature Analysis (MCSA) stands as a formidable tool in predictive maintenance, its implementation is not without challenges. One significant hurdle lies in the complexity of machinery and the diverse industrial environments in which it operates. Implementing MCSA requires a nuanced understanding of the specific intricacies of each system, posing challenges in standardizing methodologies across diverse applications. Additionally, the need for skilled personnel proficient in both the technicalities of MCSA and the unique characteristics of industrial setups adds another layer of complexity.
Limitations in Detecting Certain Types of Faults
As powerful as MCSA is, it doesn’t claim omniscience. There are certain types of faults that may elude its diagnostic grasp. Mechanical faults, for instance, may not always manifest prominently in the motor current signature, making them challenging to detect through this method alone. Understanding the boundaries of MCSA is essential, acknowledging that while it excels in certain fault patterns, it may not be the panacea for all types of issues that can afflict electrical machines.
Factors Affecting the Accuracy of MCSA Results
The accuracy of MCSA results hinges on various factors, introducing a layer of intricacy to its application. External factors such as environmental conditions, electrical noise, and variations in load can impact the precision of MCSA results. Calibration of sensors, proper installation, and the quality of data acquisition devices play crucial roles. Additionally, the dynamic nature of industrial environments introduces a level of unpredictability, requiring constant vigilance and recalibration to maintain the accuracy of MCSA predictions.
Conclusion
Motor current signature analysis has an important role in detecting possible failures. In order to detect these failures, the data must be obtained correctly and in sufficient quantity, then must be analyzed. Sensemore offers its customers the Duck solution, an IoT data acquisition device, to collect and transfer the data to the analysis software. With its 8 channels, the Duck device can take manual, periodic and triggered measurements simultaneously from 8 different analog output sensors. Analog sensors such as current, voltage, temperature, vibration, humidity, pressure etc. can be connected to these channels and the measurements can be viewed in the Sensemore Cloud App.
Fig. 4 Analog IoT Data Acquisition Device: Duck
For electrical signature analysis, Sensemore offers its customers split-core current transformers, Rogowski coils for motors with high currents; and voltage divider sensors to measure voltage values. These are easily placed on the motor phase cables in the electrical control center (panel) and the current-voltage data is transferred to the Duck device. Duck transfers this data to the Sensemore Cloud Application. Thanks to the software in the Cloud Application, this data is analyzed and reports are created for the user about possible failures, also energy monitoring is provided.
Recommended Blog Posts
September 4, 2023
Powerful Signal Analysis Tools for Vibration Analysis
Predictive maintenance, crucial for machinery reliability, heavily relies on vibration analysis. Techniques like FFT…
September 4, 2023
Rotating Machinery Vibration Analysis
Vibration analysis is a critical tool in various industries like manufacturing, power generation, and transportation.…
December 28, 2022
Fault Diagnostic Technique Using Machine Mode Similarity Analysis
AI can diagnose machine faults with vibration data but machine mode similarity analysis is an alternative, it uses…
September 15, 2022
Understanding Rotating Machinery Data
Machine data is generated by physical attributes and actions of machines, collected by sensors and analyzed for…
August 6, 2021
Envelope Analysis
Bearings are critical elements in rotating machines, they support radial and axial loads, and reduce friction. Real…
May 6, 2021
What is Cepstral Analysis?
Cepstral Analysis, a tool used to detect periodicity in frequency spectrum, can be useful in gearbox fault detection in…
October 9, 2020
How is Fault Detection Performed?
Vibration measurements and analysis, using multiple parameters, can identify developing problems in machinery before…
September 21, 2020
Parameter Selections in Vibration Measurement
Vibration measurements are used to determine the response of machines to forces and identify potential issues. It is…
September 4, 2020
What is Vibration Analysis?
Vibration analysis can be used to discover problems in machines and predict when they might fail. It can significantly…
Related Products
Sensemore Energy Monitoring Solution
If you enjoyed this blog, explore our Energy Monitoring Solution page.