Criticality analysis is an important tool used in many industries to assess and prioritize assets based on their significance to operations and safety. This methodical approach helps identify critical assets that are crucial for maintaining operations and reducing safety risks. By focusing maintenance efforts on these key components, organizations can prevent downtime and minimize potential hazards.
The value of criticality analysis goes beyond just maintenance planning. It also provides a framework for decision-making, allowing industries to allocate resources effectively. By prioritizing areas that are highly important, businesses can strike a balance between risk reduction and efficiency. Criticality analysis plays a vital role in translating theoretical risks into practical information, empowering industries to make informed choices about where to invest their maintenance efforts.
Here are some examples of how criticality analysis principles can be applied in practice:
- Using Machine Health AI for Predictive Maintenance: By leveraging advanced analytics through Machine Health AI, organizations can proactively identify potential maintenance issues before they cause any major problems. This proactive approach aligns with the core concept of criticality analysis, which emphasizes the importance of addressing high-risk areas first.
- Implementing High-Quality Data Acquisition Devices: Data Acquisition Devices play a crucial role in gathering accurate data for machine health monitoring. By investing in reliable and accurate data acquisition devices, organizations can improve the effectiveness of their overall criticality analysis strategy.
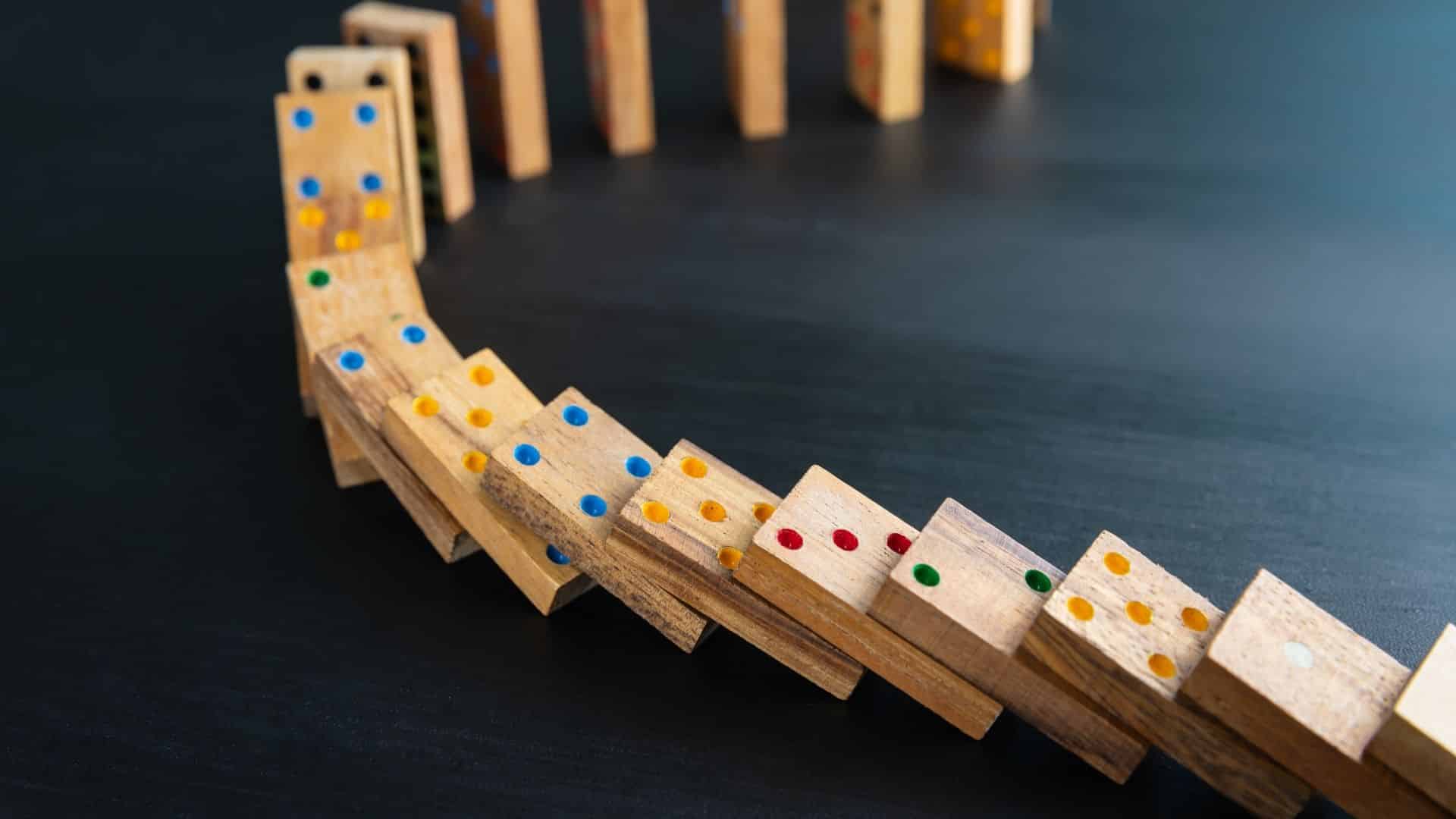
What is Criticality Analysis?
Criticality analysis is a structured and comprehensive method used to examine and rate the importance of different assets within an organization. This approach helps determine the significance of each asset in terms of its functionality, safety, and potential impact on overall operations. By assigning ratings based on criticality, organizations can effectively prioritize their resources, ensuring that the most important assets receive the highest level of maintenance and oversight.
Why Assign Criticality Ratings Based on Potential Risks?
Assigning criticality ratings based on potential risks associated with each asset is crucial for proactive risk management. It helps organizations identify and address potential issues before they escalate into major problems. Here’s why it’s important:
- Spotlighting High-Risk Assets: Criticality analysis highlights assets that pose higher risks, allowing organizations to focus their attention and resources on these areas.
- Preventing Operational Setbacks: By understanding the potential impact of asset failures, organizations can implement preventive measures to avoid operational downtime and hazardous situations.
- Optimizing Resource Allocation: Allocating budgets and personnel towards maintaining assets with higher criticality ratings ensures that resources are utilized where they can have the greatest impact.
Risk Assessment Methods Used in Criticality Analysis
1. Failure Modes Effects Analysis (FMEA)
FMEA is a step-by-step approach for identifying all possible failures in a design, manufacturing or assembly process, or a product or service. It is particularly useful in scrutinizing:
- Potential Failure Modes: Understanding how an asset might fail provides valuable information for developing strategies to prevent such failures.
- Effects on System Operations: Assessing the consequences of each failure mode allows for an evaluation of their relative impact on operations.
2. Failure Mode, Effects, and Criticality Analysis (FMECA)
Building upon FMEA, FMECA adds an extra layer – criticality analysis. This involves:
- Prioritization: Failure modes are ranked according to their significance regarding safety concerns, frequency of occurrence, detectability, and potential financial costs.
- Decision-Making Support: The combined analysis aids in forming strategic decisions about where to focus maintenance efforts.
Both FMEA and FMECA serve as crucial tools in criticality analysis by quantifying risk in terms of probability and severity. These methodologies facilitate data-driven decisions concerning asset management by systematically evaluating potential points of failure and their repercussions.
How FMEA and FMECA Work in Criticality Analysis
1. Failure Modes Effects Analysis (FMEA)
FMEA starts with listing each component or process step, identifying possible failure modes and their effects on other system components or end users. It also reviews current control measures and rates the severity, occurrence, and detection of potential failures.
2. Failure Mode, Effects, and Criticality Analysis (FMECA)
FMECA extends the analysis done in FMEA by adding a criticality score that reflects the combined effect of severity and likelihood scores. This composite score helps organizations prioritize issues based on their potential impact on operations and safety.
How Risk is Quantified through FMEA and FMECA in Criticality Analysis
The quantification involves several steps:
- Failure Mode Identification: List possible ways an asset can fail.
- Effect Analysis: Determine the consequences these failures could have on overall operations.
- Severity Ranking: Rate the seriousness of these consequences.
- Occurrence Evaluation: Estimate the probability of each
Implementing Criticality Analysis in Industries
Implementing criticality analysis is an integral part of asset management, which requires a cross-functional effort. A well-executed criticality analysis involves the cooperation and input from multiple departments within an organization, including maintenance, operations, engineering, and others. By involving stakeholders from different areas of the organization, all critical assets and potential risks can be thoroughly evaluated.
Criticality analysis is not merely a process that is carried out by a single department. It’s a methodology that requires understanding and commitment from everyone involved. This could mean providing training and education for employees to ensure they understand the importance of the methodology and their role in its success. Next-Generation Condition Monitoring Solutions can be an essential tool in facilitating this understanding.
Importance of Cross-functional Effort in Implementing Criticality Analysis
The cross-functional approach to implementing criticality analysis brings several benefits:
- It ensures a comprehensive view of the organization’s assets
- Facilitates communication between departments
- Promotes ownership and responsibility among employees
- Increases the chances of successful implementation
Roles and Responsibilities of Different Departments
In order to implement criticality analysis effectively, it’s crucial to understand the roles and responsibilities that each department plays:
Maintenance Department
The maintenance department is primarily responsible for conducting criticality analysis on assets. They determine their importance and prioritize maintenance activities based on this evaluation.
Operations Department
The operations department contributes by providing input on the operational significance of assets. Their insights into how an asset impacts production can significantly influence its criticality rating.
Health and Safety Department
The health and safety department should also be involved in the process as they are best positioned to identify assets that pose safety hazards. By prioritizing maintenance for these assets, industries can prevent accidents and uphold safety standards.
Each department brings a unique perspective to the table which enriches the criticality analysis and ensures a holistic approach to asset management.
In the Implementation Process
The process of implementing criticality analysis begins by identifying all assets and defining their functions and characteristics. Once this is done, a risk assessment is carried out based on factors such as failure modes, effects, and potential causes.
After assessing the risks, assets are ranked based on their criticality scores. This score is then used to prioritize maintenance activities and resource allocation.
Throughout this process, it’s vital to continuously evaluate and update the criticality ratings as changes occur in the operational environment or as new information becomes available.
Implementing criticality analysis is not a one-time activity but rather an ongoing process that evolves with the organization’s operations and strategic goals. This continuous attention ensures that asset management strategies remain relevant and effective.
Through cross-functional collaboration, organizations can implement successful criticality analyses that improve productivity, reduce risks, and contribute to long-term business success.
Applications of Criticality Analysis in Industries
Enhancing Asset Management with Criticality Analysis
Criticality analysis significantly impacts asset management by providing a structured approach to prioritizing assets based on their critical roles in production and safety. The process entails:
- Identification of Critical Assets: Assets are ranked according to their importance to key operations, safety, and potential impact on the business if they were to fail.
- Resource Allocation: With a clear understanding of which assets are most critical, organizations can strategically allocate resources such as staff time, budget, and materials to those that require the most attention.
- Maintenance Scheduling: Preventative maintenance schedules are developed in line with the criticality of each asset, ensuring high-priority assets receive timely maintenance.
By incorporating these steps into an overall asset management strategy, organizations can ensure that their focus aligns with the most significant contributors to operational success.
Implementing Resource Optimization through Criticality Analysis
Criticality analysis influences resource allocation decisions by:
- Prioritizing Work Orders: Maintenance tasks are ranked based on the criticality scores of the associated assets, ensuring that the most crucial issues are addressed first.
- Inventory Management: Criticality data informs inventory control practices, encouraging stockpiling of essential spare parts for critical assets and reducing excess inventory for less critical items.
- Budget Allocation: Financial resources are directed towards maintaining and improving assets that have the highest impact on operations, safety, and revenue.
This targeted resource allocation ensures that the organization’s efforts and investments yield the highest possible returns regarding reliability and operational efficiency.
Shifting to Proactive Maintenance Strategies
The adoption of proactive maintenance strategies is perhaps one of the most significant benefits offered by criticality analysis. This shift is characterized by:
- Predictive Maintenance Techniques: Using condition monitoring tools and predictive analytics to anticipate maintenance needs before failures occur.
- Enhanced Planning and Scheduling: Maintenance activities are planned in advance based on predicted needs rather than reacting to unexpected breakdowns.
- Continuous Improvement Cycles: Data from maintenance activities feeds back into the criticality analysis process, enabling ongoing optimization of maintenance strategies.
Proactive maintenance minimizes unplanned downtime, extends asset life cycles, and supports a more stable operational environment.
Achieving Operational Predictability
Operational predictability is advanced with criticality analysis by:
- Data-driven Decision Making: Leveraging historical data and predictive insights to make informed decisions about asset maintenance and management.
- Reduced Unscheduled Downtime: With improved foresight into potential asset failures, industries can mitigate issues before they lead to operational disruptions.
- Enhanced Performance Monitoring: Continuous tracking of asset conditions allows for rapid response to changes that could signify impending problems.
As a result, operations become more reliable, predictable, and capable of meeting production targets consistently.
Reducing Downtime through Prioritized Maintenance
Downtime reduction is achieved by:
- Focused Attention on High-Impact Assets: Ensuring that critical equipment is maintained properly reduces the likelihood of failure and corresponding downtime.
- Streamlined Response Protocols: When failures do occur, having predefined action plans for critical assets speeds up recovery times.
- Learning from Failures: Analyzing breakdowns in context with criticality ratings helps refine maintenance approaches over time.
Industries experience enhanced uptime by systematically applying lessons learned through criticality analysis-driven maintenance activities.
Optimizing Resource Utilization via Criticality Analysis
Resource utilization is optimized through:
- Strategic Personnel Deployment: Skilled personnel are assigned to tasks where their expertise will have the greatest positive impact on asset reliability and performance.
- Efficient Use of Tools and Equipment: Tools and diagnostic equipment usage align with maintenance schedules dictated by asset criticalities.
- Smart Capital Investment Decisions: Long-term investment strategies in new technologies or equipment upgrades focus on areas identified as high-criticality through analysis.
By judiciously deploying resources where they will be most effective, industries can enhance productivity while controlling costs.
Equipment Criticality Analysis Transformed by AI and Machine Learning
AI and machine learning have completely changed how equipment criticality analysis is done. Instead of relying on manual processes, these technologies can quickly analyze large amounts of data. This allows industries to:
- Identify patterns and trends that indicate potential equipment failures
- Predict when these failures are likely to occur
- Take proactive measures to prevent or minimize the impact of these failures through maintenance actions
How AI Improves Asset Management
One way that AI is used in equipment criticality analysis is by helping industries prioritize their assets based on real-time data. By understanding which assets are the most important for their operations, companies can make better decisions about how to allocate resources for maintenance.
This approach has several benefits:
- Cost savings: By focusing on maintaining critical equipment first, companies can avoid unnecessary spending on less important assets.
- Reduced downtime: Proactively addressing maintenance needs for critical equipment helps prevent unexpected breakdowns that can lead to costly production delays.
- Improved safety: Identifying potential issues with critical equipment early on allows companies to address any safety concerns before they become a risk.
The Role of Machine Learning in Equipment Criticality Analysis
Machine learning is another powerful tool in equipment criticality analysis. It goes beyond just prioritizing assets based on real-time data and takes into account historical information as well.
By analyzing this historical data, machine learning algorithms can:
- Identify hidden patterns: Sometimes, the factors leading to equipment failures are not immediately obvious. Machine learning can uncover these hidden patterns by analyzing large datasets.
- Predict future performance: Based on past behavior, machine learning models can make predictions about how an asset is likely to perform in the future.
- Optimize resource allocation: With a better understanding of each asset’s condition and expected performance, companies can allocate their resources more effectively.
The Benefits of Proactive Maintenance Strategies
The ultimate goal of equipment criticality analysis is to move away from reactive maintenance strategies (waiting for something to break before fixing it) and towards proactive ones (addressing issues before they become major problems).
By leveraging the power of AI and machine learning, industries can:
- Minimize downtime: By identifying potential failures in advance, companies can schedule maintenance activities at times that have the least impact on production.
- Reduce safety risks: Addressing equipment issues before they escalate helps create a safer working environment for employees.
- Increase operational efficiency: With fewer unexpected breakdowns, companies can maintain a smoother workflow and maximize their productivity.
Different Methods of Criticality Analysis
Criticality analysis offers a suite of methodologies each with distinct features suitable for different industrial applications. The choice of method depends on factors such as the complexity of the system, available data, and specific industry requirements.
FMEA (Failure Modes and Effects Analysis)
- Identifies potential failure modes for each component
- Assesses the effects of failures on system operation
- Assigns severity ratings to prioritize maintenance tasks
- Benefits: Improves reliability, helps avoid future failures
FTA (Fault Tree Analysis)
- Constructs a logical diagram that maps the pathways leading to a particular system failure
- Utilizes Boolean logic to calculate the probability of a top event based on the probabilities of its basic events
- Effective for complex systems with multiple interacting failure modes
- Benefits: Identifies root causes, supports risk mitigation strategies
HACCP (Hazard Analysis and Critical Control Points)
- Originally developed for food safety, applicable in other sectors
- Focuses on identifying critical points in a process where failure could lead to unacceptable risks
- Involves monitoring, corrective actions, and verification procedures at these points
- Benefits: Enhances product safety, assures regulatory compliance
Risk Matrix Analysis
- Uses a matrix to categorize risks based on their probability and impact
- Provides visual representation for easier prioritization
- Customizable to reflect industry-specific risk criteria
- Benefits: Simplifies risk assessment process, aids in decision-making
Pareto Analysis
- Based on the 80/20 rule; identifies the most significant factors contributing to an issue
- Helps focus efforts on changes that will have the greatest effect
- Useful for tackling a large number of problems or causes
- Benefits: Streamlines problem-solving, maximizes resource utilization
Each method enhances asset management by pinpointing crucial assets which require attention. This strategic approach contributes significantly to shifting from reactive to proactive maintenance strategies. As a result, industries benefit from increased operational predictability and optimized resource utilization while mitigating risks associated with asset failure.
By applying these methods within their maintenance protocols, organizations can preventatively address potential issues before they escalate into costly downtime or safety incidents. Such preventive measures are essential for maintaining high levels of productivity and operational efficiency in today’s competitive industrial landscape.
Integrating Criticality Analysis into Reliability Engineering Framework
How Criticality Analysis Enhances Asset Management in Industries
Criticality analysis is crucial for effective asset management in the reliability engineering framework. This approach focuses on identifying the equipment and systems that are most essential to an organization’s operations, aligning maintenance strategies with business goals. Here’s why it matters:
Key Benefits of Criticality Analysis
- Targeted Maintenance: By knowing which assets are critical, organizations can prioritize and optimize their preventative maintenance efforts.
- Resource Allocation: Resources can be allocated strategically, giving priority to high-impact assets and avoiding excessive investment in less critical equipment.
- Operational Continuity: The focus on critical assets helps minimize disruptions and maintain smooth operations, leading to improved productivity.
The Role of Criticality Analysis in Resource Allocation and Preventative Maintenance Strategies
Resource allocation is guided by criticality analysis:
- Cost Efficiency: Budgets are allocated towards maintaining assets that, if they were to fail, would cause significant operational issues or safety risks.
- Preventative Approach: Anticipatory measures are taken instead of reactive fixes, reducing the chances of downtime or safety incidents.
How Criticality Analysis Fits into Reliability Engineering Framework
The reliability engineering framework takes a systematic approach to asset management by incorporating criticality analysis:
- Lifecycle Dependability: Criticality analysis helps identify the assets that need attention throughout their lifespan to ensure reliable performance.
- Strategic Decision-Making: Integrating criticality analysis into the reliability engineering framework leads to a structured decision-making process. This method supports a company’s long-term goals by improving maintenance strategies and asset performance.
The integration of criticality analysis into the broader reliability engineering strategy achieves two main objectives:
- Proactive Maintenance: It encourages a shift from reactive to proactive maintenance strategies.
- Improved Predictability: Reliability engineering benefits from better predictability in operations due to strategic planning of maintenance activities.
By incorporating criticality analysis into the reliability engineering framework, industries can experience significant benefits in terms of operational efficiency and asset lifespan. The detailed understanding of asset importance allows for better decision-making regarding resource allocation and preventative maintenance planning—essential elements of a strong operational infrastructure.
Recommended Blog Posts
September 4, 2023
Powerful Signal Analysis Tools for Vibration Analysis
Predictive maintenance, crucial for machinery reliability, heavily relies on vibration analysis. Techniques like FFT…
September 4, 2023
Rotating Machinery Vibration Analysis
Vibration analysis is a critical tool in various industries like manufacturing, power generation, and transportation.…
December 28, 2022
Fault Diagnostic Technique Using Machine Mode Similarity Analysis
AI can diagnose machine faults with vibration data but machine mode similarity analysis is an alternative, it uses…
September 15, 2022
Understanding Rotating Machinery Data
Machine data is generated by physical attributes and actions of machines, collected by sensors and analyzed for…
August 6, 2021
Envelope Analysis
Bearings are critical elements in rotating machines, they support radial and axial loads, and reduce friction. Real…
May 6, 2021
What is Cepstral Analysis?
Cepstral Analysis, a tool used to detect periodicity in frequency spectrum, can be useful in gearbox fault detection in…
October 9, 2020
How is Fault Detection Performed?
Vibration measurements and analysis, using multiple parameters, can identify developing problems in machinery before…
September 21, 2020
Parameter Selections in Vibration Measurement
Vibration measurements are used to determine the response of machines to forces and identify potential issues. It is…
September 4, 2020
What is Vibration Analysis?
Vibration analysis can be used to discover problems in machines and predict when they might fail. It can significantly…